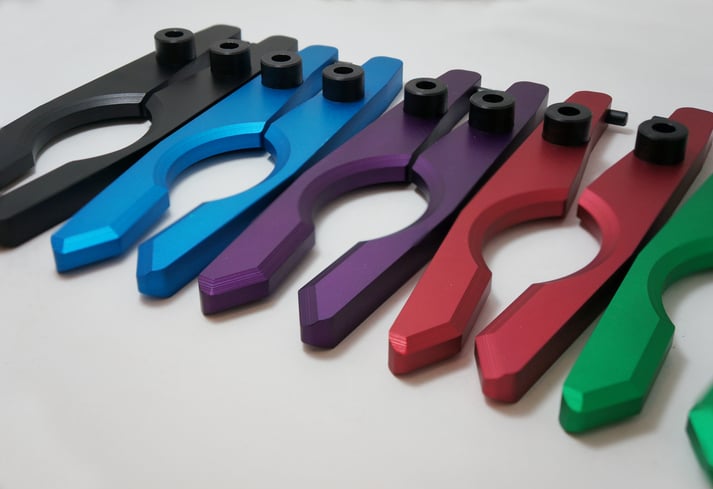
Applying surface finishing is one of the final steps in manufacturing, but one that’s critical to both the durability and aesthetics of a product. Anodizing colors is part art and part science, resulting in expertly crafted finishes that are as hardy as they are visually striking.
From aerospace components to medical devices and more, color anodizing is indispensable across all industries. As manufacturers and designers increasingly prioritize both functionality and aesthetics in their products, understanding the nuances of anodizing colors matters that much more.
And that’s why working with the right anodizing partner is so important. Anodizing color is not just applying a hue, but rather transforming the metal surfaces with a durable, vibrant finish that withstands the rigors of time and environment.
Here’s what you need to know about anodizing colors and how AOTCO Metal Finishing can support the final stages of your product.
Types of Anodizing Explained
Anodizing is a method of electrolytically enhancing the surface of non-ferrous metal – usually aluminum or titanium alloys. This process not only fortifies the material against corrosion and wear but offers a potential canvas for captivating colors.
Not all anodizing is equal. While all three types of anodizing explained below will improve durability and corrosion resistance, the properties and benefits vary.
Type I Anodizing, also called chromic acid anodizing, is the thinnest of the anodic coating processes. It creates an electrically non-conductive surface with improved scratch and corrosion resistance.
AOTCO specs for Type I Anodizing include:
- MIL-PRF-8625
- AMS 2470
- MIL-A-8625
- AMS-A-8625
Type II Anodizing, also known as sulfuric acid anodizing, is the most common method for anodization. It’s used particularly in applications where hardness and resistance to abrasion are needed, or as a base for paint systems.
AOTCO offers both Type II and Type IIB (thin sulfuric acid anodizing) with the following specs:
- MIL-A-8625
- MIL-PRF-8625
- AMS-A-8625
Type III Anodizing, sometimes called hard anodizing or hard coat anodizing, adds a greater thickness and weight compared to the other two types. It is highly abrasion resistant and non-conductive. In fact, it can make an aluminum surface harder than tool steel.
The following Type III specs are available from AOTCO:
- MIL-A-8625
- MIL-PRF-8625
- ASTM B580
- AMS 2468
- AMS 2469
- AMS-A-8625
Anodized Aluminum Colors and Aesthetic Appeal
Unlike conventional methods such as painting or powder coating, color anodization brings about a chemical transformation in an object’s surface, rather than simply adding a physical layer of color. The dye is impregnated to the surface of a substrate and then sealed post-anodizing which provides a long-lasting and durable aesthetic finish.
Color anodization can be applied to all three of these anodizing types. However, each type possesses unique characteristics that influence the coloring process because of the formation of pores on the surface of the oxide layer during anodization. These pores vary in their frequency, depth and width, and so interact with dyes in different ways. This results in variations in color intensity and appearance.
In particular, Type III hard coat anodization has more limited dyeing capabilities because of its thicker oxide layer.
Popular Anodized Colors and Applications
Custom colors on anodized aluminum surfaces are not only about aesthetics but functionality, providing visual cues for identification or branding. Here are some of the most popular anodized aluminum colors and their applications:
- Clear/Silver: Clear or silver anodizing is a versatile choice that maintains the natural appearance of aluminum while providing enhanced durability and corrosion resistance. It is widely used in architectural applications, electronics and automotive components where a sleek, metallic finish is desired.
- Black: Black anodizing offers a sophisticated and modern appearance while providing excellent UV resistance and corrosion protection. It is often chosen for architectural elements, consumer electronics, satellite components and automotive accessories.
- Blue: Blue anodizing ranges from subtle pastel shades to vibrant cobalt hues, offering versatility in design. It is used in aerospace components, the medical industry and consumer electronics where a more distinctive finish is desired.
- Red: Red anodizing adds a bold and eye-catching accent to aluminum surfaces, making it ideal for automotive parts, medical device components and fashion accessories. It can also be used in signage and branding applications to create impactful visuals.
- Green: Green anodizing is valued for its natural and refreshing appearance, making it suitable for architectural elements, medical parts and eco-friendly product lines. It can evoke associations with sustainability and environmental consciousness.
- Gold: Gold anodizing lends a luxurious and decorative finish to aluminum surfaces, making it a popular choice for jewelry, decorative hardware and high-end consumer products. It is also regularly used in aerospace and automotive applications.
- Custom Colors: Beyond standard options, custom anodizing colors allow for endless possibilities in design and branding. AOTCO can match your corporate colors, create unique color gradients or experiment with innovative finishes to differentiate your products in the market.
Anodizing for Specific Metals
Anodizing Aluminum: Techniques and Tips
Aluminum is the prime candidate for anodizing because of how compatible the metal surface is with anodizing and coloring methods. The resulting anodized coatings on aluminum materials provide a layer of protection that is both functional and attractive.
When anodizing aluminum, several techniques and tips ensure optimal results:
- Surface Preparation: Proper surface preparation is essential to achieve uniform and high-quality anodized coatings. This involves thorough cleaning to remove any contaminants, oils or residues that may interfere with the anodizing process.
- Anodizing Parameters: Control of anodizing parameters such as voltage, current density and electrolyte composition is critical to achieving desired coating thickness and color consistency. Fine-tuning these parameters allows for precise control over the anodizing process and the resulting surface properties.
- Dyeing Techniques: For colored anodizing, selecting the appropriate dye and dyeing technique is critical. Proper dyeing techniques ensure vibrant and durable coloration that withstands environmental exposure.
- Sealing Process: Sealing the anodized coating is crucial for enhancing its corrosion resistance and durability. Proper sealing ensures long-term performance and maintains the aesthetic integrity of the anodized surface.
- Post-Treatment: Laser markings, engravings, chemical films and hydrogen embrittlement stress relief are just some of the post-treatments available.
- Quality Control: Implementing rigorous quality control measures throughout the anodizing process helps identify and rectify any deviations or defects early on. This includes regular monitoring of process parameters, thorough inspection of finished parts and adherence to industry standards and specifications.
Beyond Aluminum: Anodizing Magnesium and Titanium
While aluminum is the most common material for anodizing, other metals like magnesium and titanium can also undergo a similar electrolytic finishing process to achieve an anodized coating.
Magnesium anodizing takes the naturally occurring oxide layer on the metal’s surface and chemically builds a protective layer on the surface of a magnesium substrate. This greatly improves the anti-corrosion properties, physical strength and adhesion capabilities for dyes. Anodized magnesium has applications in numerous industries including aerospace, defense and medical thanks to its high strength-to-weight ratio, wear resistance and ability to be sterilized.
Similarly, titanium anodizing (Mil Spec AMS 2488) is also often used in aerospace, defense, automotive and medical applications. Titanium anodized parts are biocompatible, resistant to wear and anti-corrosive. Type III anodized titanium in particular offers a range of colors for aesthetic appearance, including silver, bronze, purple, blue, light blue, gold, rose, magenta, teal and green.
Common Questions on Color Anodizing
What is the difference between Type II and Type III anodizing?
The primary difference is the thickness and properties of the oxide layer formed during the anodizing process. Type II anodizing produces a thinner oxide layer that enhances appearance and provides some level of corrosion protection. Type III anodizing, also known as hardcoat anodizing, creates a thicker, denser oxide layer that significantly increases the material's wear and corrosion resistance.
Can anodizing colors fade over time?
Anodized aluminum colors are remarkably stable due to the dye being sealed within the porous oxide layer. However, prolonged exposure to UV light can cause some colors to fade over time. Red and blue hues are particularly susceptible to fading, while black and darker colors tend to be more UV resistant.
What are the applications for anodized aluminum?
Anodized aluminum is used in a wide range of applications due to its enhanced durability and aesthetic appeal. Common applications include architectural components, consumer electronics, kitchenware, aerospace parts and medical devices.
Does anodized aluminum corrode?
Anodized aluminum is highly resistant to corrosion, making it a preferred choice for applications where durability and longevity are paramount. The anodizing process creates a protective oxide layer on the surface of the aluminum, which acts as a barrier against corrosion and oxidation. This oxide layer is formed through an electrolytic process that thickens the naturally occurring oxide layer on aluminum, making it harder and more resistant to environmental factors.
Can anodized aluminum be welded?
Welding anodized aluminum requires removing the anodized layer around the area to be welded, as the oxide layer does not conduct electricity well and can contaminate the weld. After welding, the part can be re-anodized to restore corrosion resistance and aesthetic appearance.
Choosing the Right Anodizing Partner
Partnering with AOTCO means gaining access to a trusted team invested in your project's success through delivering results that exceed your expectations. Our team of senior anodizers, platers and engineers have decades of experience providing consistent and quality color anodizing, as well as other metal finishing solutions.
Reach out to us today to learn more about how we can help you achieve your metal finishing goals with confidence and precision.