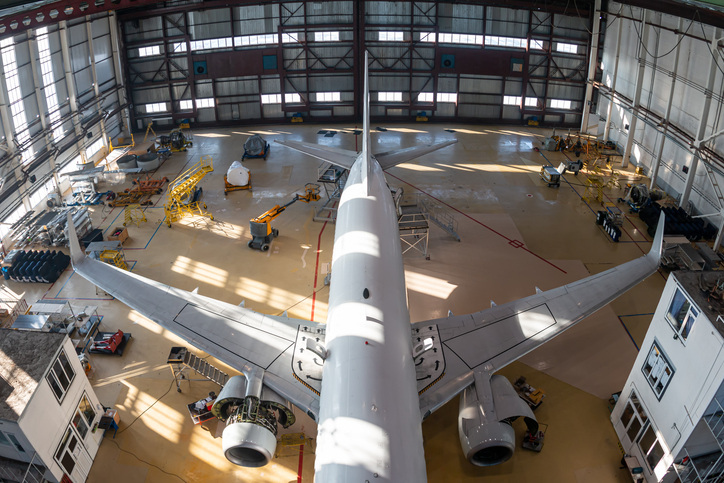
In industries like aerospace, aviation and electronics – where component reliability is critical – protective finishes such hot solder dip are incredibly beneficial. AOTCO is excited to announce that we now offer tin dip solder services, adding to our portfolio of other advanced metal finishing solutions.
As one of the few companies in the United States capable of performing these operations, we are pleased to offer our clients a proven method for improving solderability and long-term corrosion resistance for parts in harsh, high-stress environments.
What Is Hot Solder Dip?
The terms hot solder dip, hot tin dip (or hot tin dipping), tin reflow and flow brightening are sometimes used interchangeably, but there are some key differences between these processes.
Hot solder dipping involves immersing components into a molten bath of tin-lead alloy (typically a 60/40 split) at temperatures exceeding 370°F. This forms a durable protective coating that is made up of a thin intermetallic compound layer at the base, followed by a thick layer of pure solder.
Hot tin dip is similar, but the part is immersed in a molten bath of pure tin, which has a higher melting point at 450°F.
Tin reflow, or flow brightening, is a secondary process where a previously plated or dipped layer of tin (or tin lead) is heated again until it reflows, or melts slightly, to create a smoother, sealed finish. This helps improve the surface finish and helps mitigate any imperfections in the original plating.
This is, of course, distinct from other metal finishing services like tin electroplating that involves applying a tin coating through an electrochemical process – that is, where an electric current deposits tin onto the component. Electroplating typically results in a thinner, more controlled coating but it's more porous and less durable relative to hot dipping.
Also, electroplated coatings are more prone to oxidation and tin whiskers, which is why hot dipped tin is a more reliable option for harsh environments.
Why Choose Hot Solder Dipping?
Hot solder dipping offers numerous advantages that make it the preferred choice for applications that need robust protection.
Key benefits include:
- Enhanced Solderability: Components coated with hot solder dip are easier to solder compared to pure tin finishes because the lower melting point of the solder allows for a variety of heating methods at different elevated temperatures.
- Corrosion and Oxidation Resistance: The protective coating protects the part from rusting or oxidizing. This makes it ideal for use in harsh environments, such as aerospace and defense applications, where components have to withstand extreme conditions for long periods of time.
- Whisker Mitigation: Tin whiskers – that is, tiny metal hairs that can grow on tin plating and cause electrical short circuits – are a major concern in the electronics industry. Adding lead to the solder alloy or using tin reflow processes helps eliminate whiskers, ensuring longer-lasting reliability for sensitive electronics.
- Flexibility and Durability: Unlike electroplated coatings, dip solder finishes are less porous, more ductile and better able to withstand mechanical stress, such as flexing and vibration, without cracking. This is especially important in industries like aviation, where components have to maintain their structural integrity under constant movement.
While hot solder dipping offers many advantages, it does have some limitations. The coating thickness is less precisely controlled compared to electroplating methods, which can make it less suitable for applications that need extremely tight tolerances. It should also not be used when the base part has fine details that could be obscured by a thicker plating layer.
Long-Term Performance and Durability
The biggest advantage of parts and equipment that has been through a dip solder process is the long-term durability and reliability of those parts compared to regular tin lead plating or electroplating. Components treated with hot tin dip remain solderable for up to 15-20 years, far outlasting traditional tin-lead coatings, which may degrade after just a year.
For example, a member of the AOTCO team recently inspected a client’s warehouse located near a humid estuary on the East Coast. Remarkably, parts that had been stored there for over 15 years in a damp, muggy environment remained perfectly solderable – speaking directly to the long-lasting durability of our hot solder dip process.
Hot solder dip is an excellent choice for parts exposed to high temperatures, environmental stresses or corrosive conditions, making it the ideal solution for industries that demand long-term reliability and robust performance.
AOTCO, Your Trusted Partner for Long-Lasting Metal Finishing
At AOTCO, we pride ourselves on delivering finishing solutions that stand the test of time. Our hot solder dip – and all our services – are engineered to provide unmatched durability and reliability. Whether you're in aerospace, defense, electronics, or any industry requiring reliable finishes, our team is here to meet your needs.
Get in touch with us today to tell us about your hot solder dipping needs.