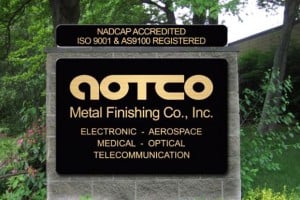
What is Electroplating Thickness?
Electroplating is the process of applying a thin layer of metal or metal alloy on the surface of another metal, alloy, or other material. Used for both aesthetic and practical purposes, Electroplating is a commonly used process in a variety of manufacturing industries.
One key element of the plating process is the electroplating thickness. The thickness of electroplating usually ranges from 0.0001 inch to 0.020 inch. While these may seem like small measurements, even the slightest build-up of thickness can provide great durability and corrosion resistance.
Electroplating Thickness Control
Controlling the thickness of your material is a crucial skill for most industrial, military, or commercial applications. When electroplating, the thickness of the metal coating is going to be entirely dependent on the length of time the part spent in solution. However, electroplating is influenced by many variables such as the solution, temperature, metals, current, and more. Necessarily, the bath will need to be calibrated to your specific conditions. The best way to do this is empirically.
Be sure to consider the optimal temperature, concentration, and voltage conditions. Like all electroplating, both your parts will need to be cleaned carefully prior to plating.
Electroplating Complex Geometries
Keep in mind that the complexity of the device’s dimensions will inform how to develop a mathematically perfect and even coating. This is why your reference piece should be as close to your showpiece as humanly possible. Additionally, not all metals are as flexible when it comes to plating complex shapes or tolerating voltage variances.
Why is Plating Thickness Important?
Electroplating provides a variety of ranging qualities to the material it encases. Oftentimes these qualities are determined by the thickness of the plating. The plating thickness of an object is directly proportional to its durability. Aside from increased strength, plating thickness can also determine a substrates corrosion resistance capability. For decorative plating, thickness can often affect the physical appearance of the object. When plating chrome or gold for decorative purposes, there will be a minimum thickness applied in order to keep the lustrous shine of these metals.
What Causes Irregular Thickness?
Irregular plating thickness can appear in a few different ways for a variety of reasons. Often, irregular thickness is due to complications during the process or with the electroplating bath. Insufficient plating can happen if the bath does not have an adequate number of metal ions compared to the catalyst. This deficiency can cause uneven coverage of the part and even full part failure.
Overstabilization can also cause irregular thickness, specifically during the electroless nickel plating process. These stabilizers are used to keep nickel in the bath solution, however if overabundant they can cause an uneven spread of nickel on the substrates surface.
Excess build-up can occur due to a substrate’s complex geometries. Excessive build up usually occurs if proper testing is not done on test parts prior to the procedure. For example, if a shape has sharp corners, holes or varying curvatures, extra attention will be required during the plating process to ensure even thickness.
Consequences of Excessive and Insufficient Thickness
Excessive Thickness
- Cracking: Excessive coating can cause internal stress and cause cracking
- Roughness: Excessive thickness can cause the surface of an object to become rough making it hard to apply secondary layers
- Peeling: Coatings that are too thick become brittle and eventually start to peel off
Insufficient Thickness
- Rusting: When the coating is too thin to provide sufficient protection, rusting can occur in areas where coating is unevenly applied
- Cracking: an insufficient thickness can cause the surface to be weak, brittle, & eventually crack
- Void: When coating is insufficiently applied it can cause the surface of the component to remain visible. This phenomenon is called a Void. Voids increase the risk of corrosion or abrasion, as well as take away from the component’s aesthetic appearance.
At AOTCO, we have a team of engineers and platers ready to solve your metal finishing needs, no matter how complex. Let us know how we can help you with your next project. Contact us at 800-275-0880 for more information!